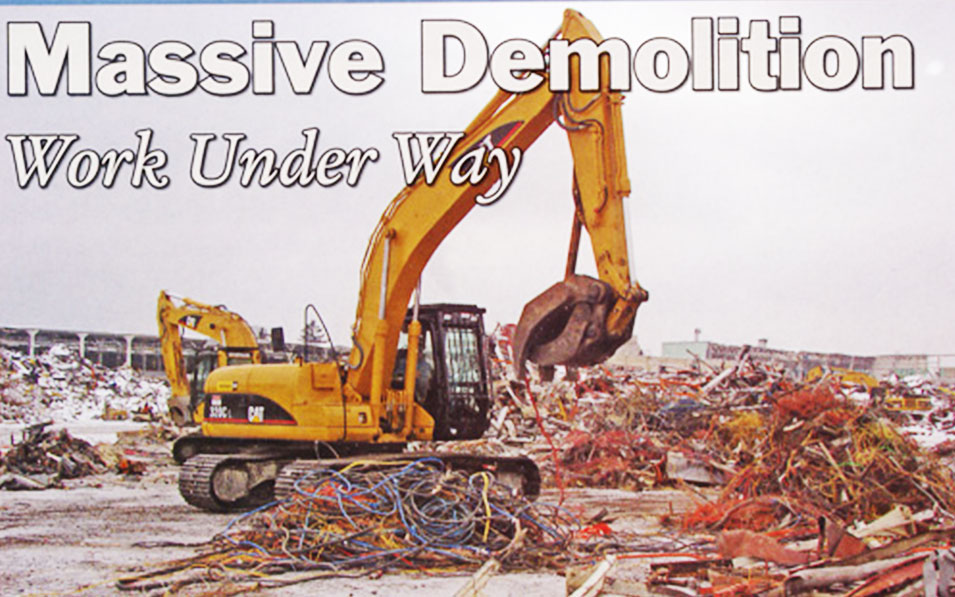
25 Jul Two GM Plants – Demolition and Replacement
Two General Motors Corporation plants in Lansing are being demolished, having been replaced with state-of-the-art facilities. Demolition work began in January 2006 and substantial completion is expected in May.
“The two plants that we are demolishing are the Fisher Body Plant, which was Plant Six and Oldsmobile Plant One. Oldsmobile Plant One was approximately 3.4 million square feet and Fisher Body was approximately 3.1 million square feet. Most of this was built from 1906 to approximately 1965,” David Mardigian, president of MCM Management Corporation, of West Bloomfield Township, said.
“Both plants made high-quality product, but the cost of operating the facilities in a safe and environmentally correct way was becoming prohibitive. They couldn’t compete with the corporation’s forward plans for safety, product quality and productivity.
“When the new Cadillac and Delta Township plants opened, MCM was hired to demolish the old plants. Our job for General Motors is to perform environmental cleaning, remove all asbestos, demolish the buildings, and recycle everything possible. We recycle between 92 percent and 97 percent of materials for General Motors projects. We believe that we will recycle approximately 95 percent of these plants. This is a mandate from General Motors and it’s one of our core competencies.”
Before demolition work begins, General Motors removes any assets needed by other General Motors plants. Therefore, most usable assets are gone before demolition work begins. “In the event that they leave something behind that is non-proprietary and reusable, we will sell it for reuse, but this is not the norm. Most of the material, including the structures themselves, are recycled as scrap,” Mardigian said.
Mardigian pointed out that metallic and non-metallic materials are pushed into the scrap recycling stream. Most of the steel scrap is processed on-site and goes to steel mills. This gives General Motors maximum value for the scrap.
Non-ferrous metals, such as copper, stainless steel and brass are also processed on-site and sent to either smelters or an off-site processor for final processing before it can go to a consumer.
“After we have handled all of the steel, ferrous and nonferrous scrap materials, we then have some plastics and some wood that can be recycled,” Mardigian said. “What we can’t reuse, scrap or salvage is waste. This is usually roofing material, insulation and wood products that have outlived their usefulness. This material is between 2 percent and 5 percent of the total material.
“We’re running approximately 50 machines, 90 percent of which have a non-traditional work tool on the end of them. Those tools allow us to do a number of things. Number one, we are able to remove the building in total safety.
We do not have people on the ground with cutting torches to assist in the demolition process, which has allowed MCM to have an industry-leading safety record.
“We don’t hurt people on our demolition projects because we’ve taken the manual demolition tasks and transformed them into mechanical operations. We’ve taken many of our laborers and trained them to become machine operators. This gives us increased productivity and safety.
“So, as the buildings are taken to the ground with demolition shears or concrete demolition tools or pulverizers, a segregation process starts. After the building hits the ground, we separate the building materials. Grapples and shears remove the steel and feed that into stockpiles where the shears will be making scrap for the steel mills.
Grapples and loader buckets will grab the lighter material that is sheet iron and place that in our baler. “The same machines will put the concrete in a pile and take the lower grade scrap such as rerod and put it in different piles for further processing and they will recover the non-ferrous materials.” Magnet machines are also involved in this process.
MCM controls most of its own transportation, other than railroad transportation. “This gives us the ability to react with these work tools. We can take an emergency order from a mill and make 1,000 tons to 2,000 tons of scrap to their specifications, load it with our magnets, cut it with our shears, haul it with our trucks, and get to a mill within 100 miles of an MCM job in a hurry,” Mardigian said.
“Even the waste material gets worked on by attachments. Shears cut the big unwieldy material in order to make better density and reduce our transportation costs. The grapples will load it and sift through it and when we’re all done, it goes on MCM trucks and to the landfill.” The last part of the stream is concrete recycling. MCM owns a Lippmann concrete crusher that crushes 4,000 tons of concrete per day. This is the end of MCM’s recycling process.
“Seventy-five percent of our tools are excavator mounted. The wheel loaders we own include Cat 950s, Cat 980s, Cat 988s, and Volvo 110s and 220s. The excavators we own include 320 to 385 Cats, and EC140 to EC460 Volvos. Ninety-five percent of our excavators have a demolition shear, scrap shear, grapple, or a concrete pulverizer on them,” Mardigian said.
“Some shears are good for taking the building down, but they could also be used to prepare the scrap. We own approximately 50 shears, approximately 44 of which are LaBounty. The other five or six are Caterpillar multi-processors. Our LaBounty shears range from MSD1000, which fits on a Cat 315 and on our ultra-high demolition machine, a Cat 345 UHD, all the way up to an MSD9500, which cuts with over 5,000,000 pounds of force and weighs 40,000 pounds. We also own LaBounty UP25 shears, which fit on Cat 325, Cat 330 and Volvo machines; and a UP 35, which fits on Cat 330 and Cat 345 machines. “We own approximately 10 concrete pulverizers. Some are for cutting down monstrous concrete buildings with huge rerod inside and some are for processing at the crushing facility. We also own approximately 40 LaBounty grapples. They have a variety of functions. They have a demolition function, a sorting function and some are rotating grapples.” Mardigian pointed out that the work tools and the machines must be integrated.
Sorry, the comment form is closed at this time.